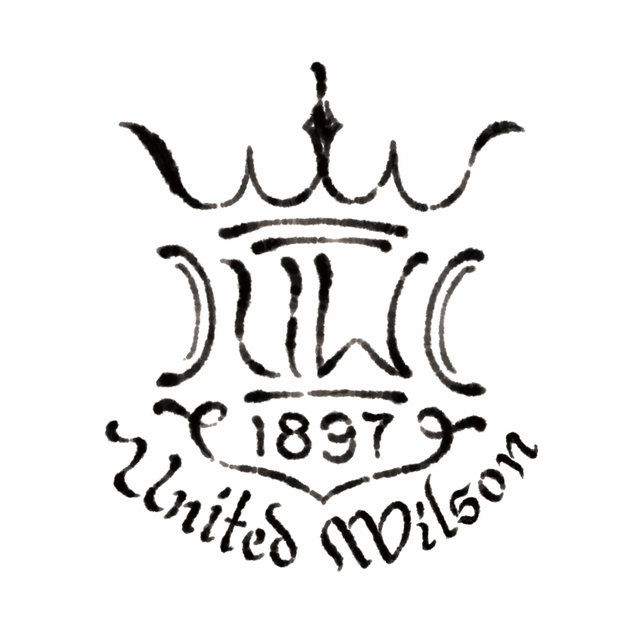
Our Foundation
Since our founding, UWPF has lived by a single guiding principle - excellence in everything we do. This means that every piece we create is crafted with the utmost care and attention to detail. For us, it's not just about making beautiful things - it's about taking pride in our work, knowing that our creations will be treasured by generations to come. This is our standard, our way of life, and our legacy.
What is Porcelain?
Ceramics, earthenware, stoneware and porcelain are some terms that are widely use, but hard to tell apart by non professional.
In general, ceramic is a blanket term that covers earthenware, stoneware, porcelain and several others. Though all are made from clay extracted from earth, they differ in composition as well as physical characteristics.
What makes porcelain special is that a specific kind of clay known as Kaolin is used. Blended with a specific mix of minerals, the clay is fired under a very high temperature at about 1400°C - 1450 °C (i.e. ~2650 °F). This makes porcelain denser, stronger and more durable than other ceramics, whilst having a fine texture and translucent appearance that makes it perfect for fine dinnerware and decorative items.
Preparing, Shaping and Drying
In UWPF, we only works with porcelain. It arrive our facility as a grayish moist formless raw clay. Stiff and hard to manipulate, the raw clay is carefully mixed with water to form a smooth, pliable material that can be shaped into the desired form. For making intricate details like hand-sculpting a delicate porcelain flower, the clay is blended with organic additives and mature in the aging room to reach the right plasticity for sculpting.
Using combinations of hand-tools and molds, our sculptor & shaper would fashion the clay into desired shape. In UWPF, we place strong emphasize on aesthetic proportion & curvatures. Our rigorous standard often means most sculptors & shapers would go through almost one year of training phase before his/ her work would be usable. Once shape is set, the clay body will be sent to a dedicated room for air drying, which takes days or even weeks depending on size and weather god. Larger pieces on humid season require much longer time to dry thoroughly, but patience is imperative in this process because excess moisture remains within the clay can cause the piece to deform or blow out completely during firing.
Once moisture is largely evaporated, the once grayish colored clay body is now off white in colour. After a final round of polishing to remove any surface blemishes and a final checking on dryness, it is ready for firing.
First Firing (Bisque Firing)
A kiln master's job is demanding because it is a combination of physical work and technical understanding of porcelain's behavior under extreme high heat.
Before firing, a kiln master would examine the size, thickness and shape of the pieces to be fired.
Based on this attribute, it determine how each piece would be placed inside the kiln, ensuring balanced & graduated rise in temperature inside the kiln to avoid deformation or blow out.
Support structure will be added to fragile or heavy pieces that are more prone to deform. Each piece will then be carefully placed onto a multi-tiered trolley in corresponding position and ready to be loaded into the kiln for firing.
Once the trolley is loaded and pushed inside the 6 feet tall tunnel shaped kiln, the kiln door is sealed close, leaving only a small opening at the kiln door known as peephole. This peephole not only allows the kiln master to monitor the firing process, but also allow some fresh air to go in and what little moisture left in the air to escape. With a time-tested firing schedule that determine speed of temperature raise and duration, the first firing commenced. With the peephole, the kiln master checks the pyrometric cones placed inside the kiln to help gauge whether sufficient temperature is reached inside. Sometimes, micro adjustment is needed according to the kiln master's experience. As temperature gradually reaches 1000-1200 °C (the peak temperature for bisque firing), the clay body hardens and any residual moisture will be lost.
Once the kiln is gradually cooldown, the clay body is transformed into a bisque - an unglazed form of white porcelain. Left unfinished, bisque is an art form in itself, perfect for accentuating details of a sculpture or figurines.
Glazing, Painting and Final Firing
To turn bisque into the glossy colorful porcelain as we know it, a glaze is used. Glaze comes in multitude of colour. Nuanced and infinite in possibility like colour itself, some glaze can even produce kaleidoscope like visual effect. But its uses is not only for decoration, glaze also act as a protective layer from damage. Each glaze have their own specific firing temperature, once fired, the glaze become vitreous, harden and fused with the bisque.
The process of firing a glazed porcelain is similar to bisque firing, but it is one of the most important and technically challenging step in porcelain firing process. After loading the glazed porcelain into the kiln, it is fired to temperature ranging from 800°C to 1450°C. However, some glaze is more particular in firing such as the elusive oxblood red.
Oxblood Red, known as the Sang de Boeuf glaze, is priced by collectors not only because it is valuable for its use of gold in its formulation, but also firing it require precise firing control as well as specialized kiln & equipment. As the firing reaches peak temperature, the kiln master will shut off the peephole to seal off any incoming air. This creates a low oxygen atmosphere within the kiln whereby even oxygen molecules present in the glaze is being reduced. Any deviation in the temperature would result in a brownish dull colour rather than the elusive deep oxblood red that collectors so sought after. This particular complex process is known as "Reduction Firing".
Beside some special glaze, painting porcelain with patterns present another technical challenge, because multiple colour glaze is used whilst some glaze is fired at different temperature and some cannot be mixed with another due to incompatibility. To paint an elaborate patterns and circumnavigate this issue, a porcelain painter needs to push technical boundaries to extreme by painting & firing layers of colors separately. In UWPF, a porcelain piece may take up to 4-5 firing session by the end.
With such complex process, it is often said porcelain is one of the most technically challenging form of art to master, but its paradoxical strong & fragile beauty and time tested quality are what makes UWPF's porcelain more special than other ceramics.
United Wilson Porcelain Fty.
Flat D, 11/F, Block 2, Kingley Industrial Building,
33 Yip Kan Street, Wong Chuk Hang
Hong Kong